Customized Metel Sanders
Metal sander supports full range of customization to meet different needs. Our metal sanders are known for their high degree of flexibility, from models to sizes to industry applications, all of which can be customized to meet your needs. Whether you are producing small precision parts or large metal structures, we can provide you with the perfect solution.
1. Choice of different models
- Basic model: Suitable for small batch production or basic machining needs in a laboratory environment, easy to operate and cost-effective.
- High-efficiency model: for medium to high production demand, supporting continuous batch production, suitable for medium-sized factories and production lines.
- Professional: Equipped with advanced automation system, suitable for high-precision and high-efficiency professional processing scenarios.
- Multi-functional type: integrating sanding, polishing and chamfering, meeting the demand of complex process and reducing the investment cost of equipment.
2. Machines of different sizes
- Small sander: designed for processing small-sized workpieces, widely used in electronic parts, hardware accessories, home decoration parts and other fine processing areas.
- Medium-sized sander: suitable for processing medium-sized materials, such as metal plates, profiles, tubes, to meet the daily production needs of most factories.
- Large sander: designed for large metal plates or structural parts, such as ship parts, construction materials, with extra wide working table and high load capacity.
3. Adaptation for different industries
- Sheet metal processing industry: Provide efficient solutions for welding seam leveling, burr removal and surface polishing of sheet metal.
- Automobile manufacturing industry: customized for high-precision processing of automobile parts, such as car frame, engine shell, etc.
- Home appliance industry: adapted to stainless steel, aluminum alloy shell drawing and surface treatment, to enhance the product texture.
- Aerospace industry: high-strength metal sanding for aviation components to ensure surface finish and processing precision.
- Metal furniture industry: provide efficient polishing and chamfering solutions for metal products such as tables, chairs, cabinets, etc. to enhance the appearance and feel.
4. Advantages of customized services
- Flexibility: Design the most suitable equipment according to customer’s material characteristics, processing technology and production scale.
- Modular design: Different functional modules, such as chamfering unit, drawing unit, etc., can be optional to realize multi-purpose use of one machine.
- High efficiency: Tailor-made equipment ensures the best processing results, while improving production efficiency and reducing labor costs.
- Intelligent control: Supports automation and digital management for easy production line integration.
- Regardless of your industry, processed material or production scale, we are committed to providing you with high-performance, cost-effective metal sanding solutions to help your business reach new heights!
Regardless of your industry, processed material or production scale, we are committed to providing you with high-performance, cost-effective metal sanding solutions to help your business reach new heights!
Model | MS-R-R400 | MS-R-R630 | MS-R-R1000 | MS-R-R1300 | MS-R-R1600 |
Width | 400mm | 630mm | 1000mm | 1300mm | 1600mm |
Thickness | 0.5-100mm | 0.5-100mm | 0.5-100mm | 0.5-100mm | 0.5-100mm |
Speed | 0-25m/min | 0-25m/min | 0-25m/min | 0-25m/min | 0-25m/min |
Diameter | 140mm | 160mm | 190mm | 210mm | 240mm |
Motor | 12.47kw | 16.87kw | 23.87kw | 48.37kw | 49kw |
Pressure | ≥0.55Mpa | ≥0.55Mpa | ≥0.55Mpa | ≥0.55Mpa | ≥0.55Mpa |
Dimension | 1400x900x1600mm | 1700x1150x2000mm | 2000x1600x2100mm | 2350x2450x2100mm | 3000x2100x2100mm |
Weight | 900kg | 1200kg | 1800kg | 1800kg | 4000kg |
Default voltage | 3 phase 380v 50MS | ||||
Sand frame | Sanding belt and wheels can be customized |
Different abrasive belts, chamfering wheels and polishing wheels for different processes.
The configuration of multi-pass sanding can be flexibly matched according to the material of the workpiece, surface requirements and processing process needs to achieve the best processing effect.
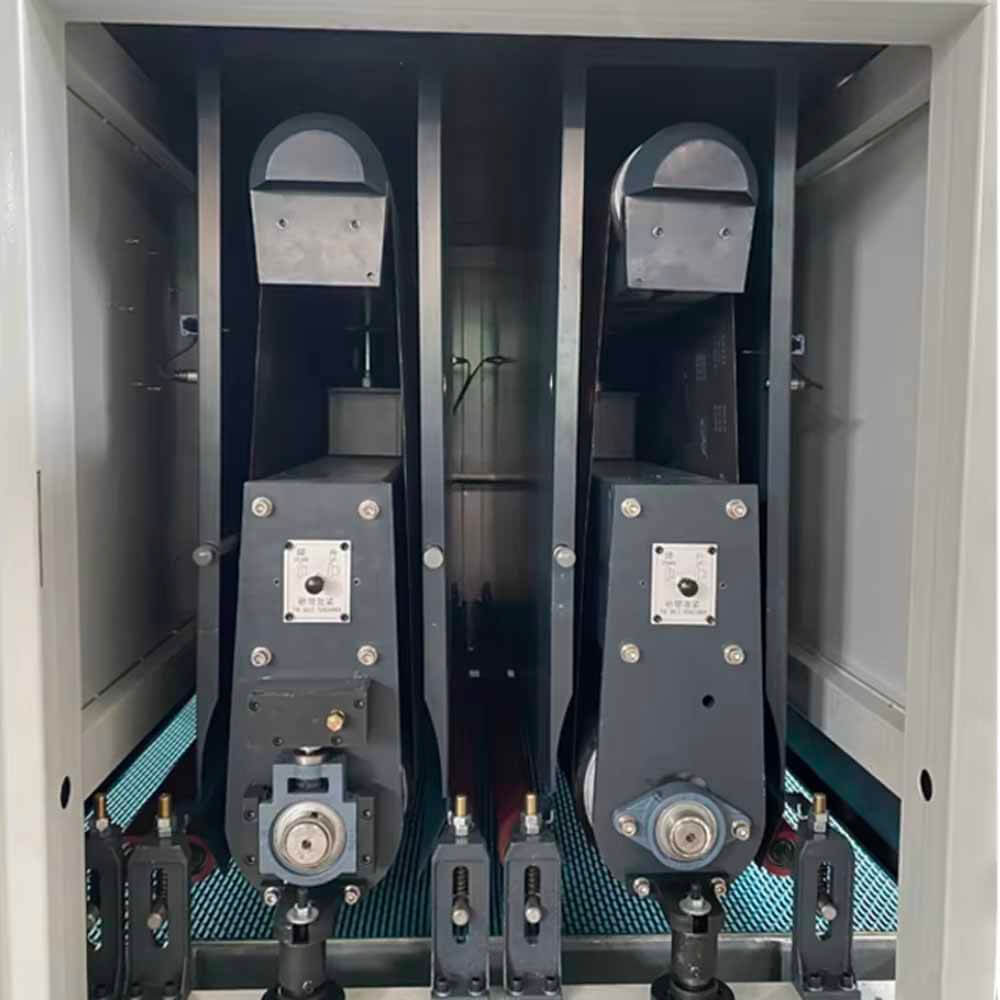
Basic combination: coarse sand + fine sand
Applicable scenes: deburring, preliminary leveling of the surface.
Configuration:
First course: coarse sanding (40-80 grit sanding belt), quickly removing weld seams, burrs or oxidized layer, significantly improving surface flatness.
Second pass: fine sanding (120-180 grit belt), refines rough texture in preparation for subsequent polishing or painting.
Characteristics: Economical and efficient, suitable for processes that do not require high surface finish.
Standard Configuration: Coarse Sanding + Medium Sanding + Fine Sanding
Applicable scenarios: Mid-range processing that requires further improvement of surface smoothness.
Configuration:
First course: coarse sand (40-80 grit belt), removing surface impurities and large unevenness.
Second course: medium grit (100-120 grit belt), uniformly refining the surface texture and eliminating traces of rough sanding.
Third course: fine sanding (180-240 grit belt) to create a more delicate surface in preparation for polishing.
Features: well-balanced, suitable for most metal processing needs.
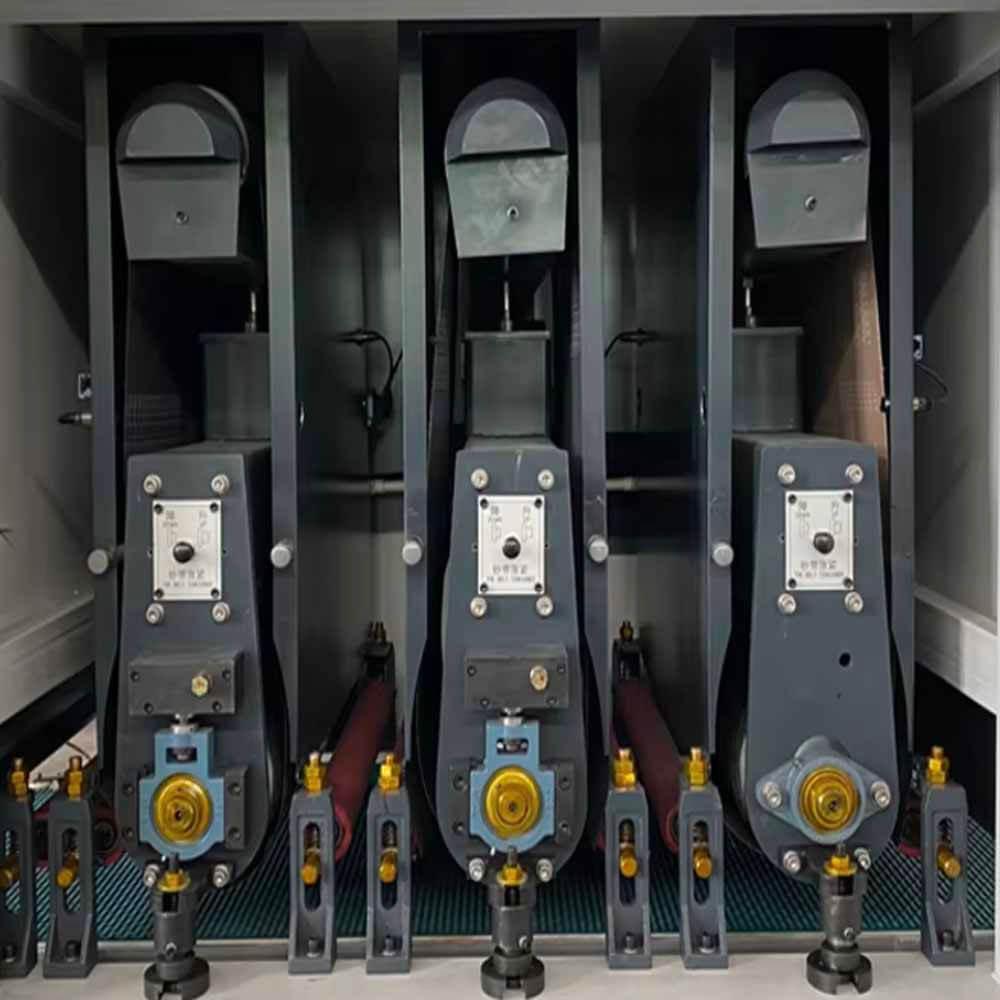
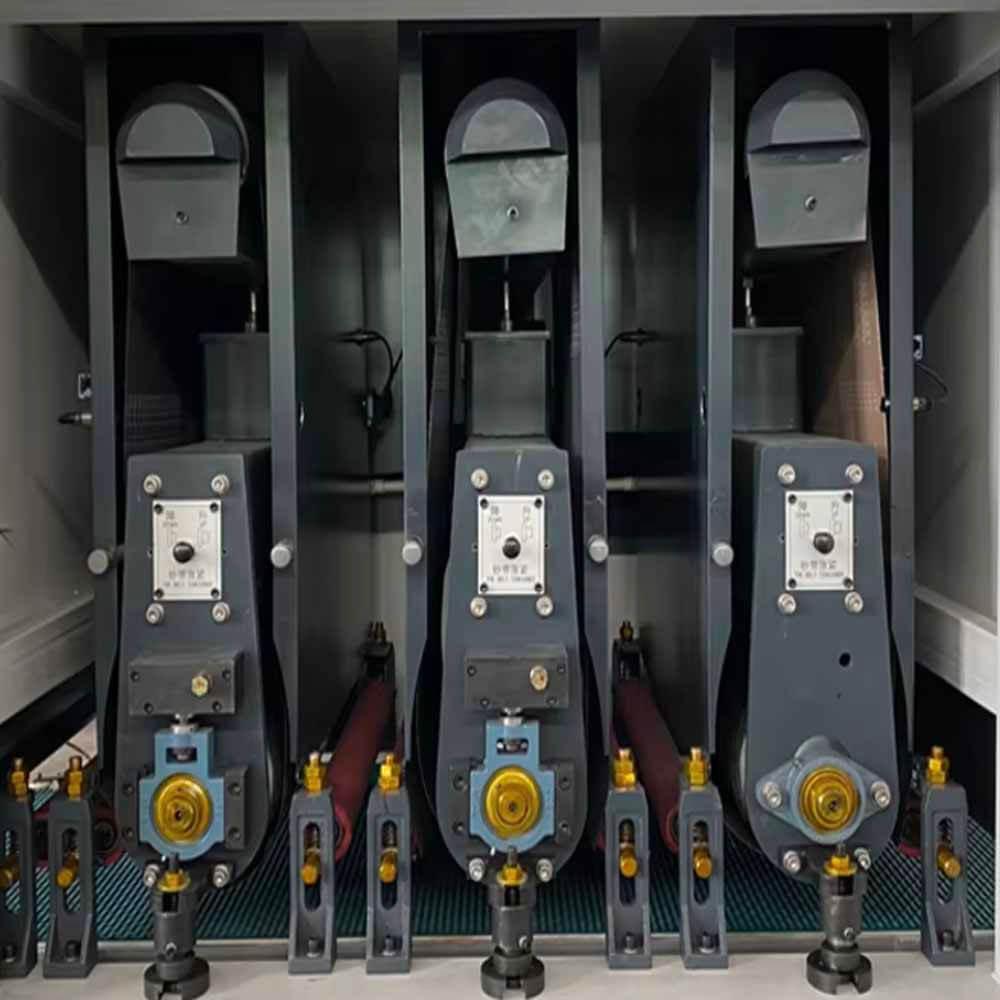
High precision with: multi-pass fine sanding
Applicable scenario: Processing that requires very high surface finish, such as high-end decorative plates, stainless steel kitchenware.
Configuration:
First pass: medium sand (120 grit belt), eliminating rough surface and preliminary finishing.
Second course: fine sand (180 grit belt), further refine the surface texture.
The third course: super fine sand (240-400 grit belt), to create a smooth and delicate high-gloss surface.
Characteristics: Suitable for processes requiring a high gloss or mirror effect, usually used in combination with the polishing function.
Multi-functional combination: coarse sanding + medium sanding + brushed sanding
Applicable scenes: products that need both flat processing and brushed texture decoration, such as stainless steel panels, elevator decorative panels.
Configuration:
The first course: coarse sand (40-60 mesh sand belt), quickly remove large burrs and unevenness.
The second course: medium sand (100-120 mesh sand belt), optimize the texture, to ensure a uniform surface.
The third course: brushed sand (special brushed sand belt), forming a uniform and beautiful brushed texture to enhance the decorative effect.
Characteristics: Take both functional and decorative processing needs into account.
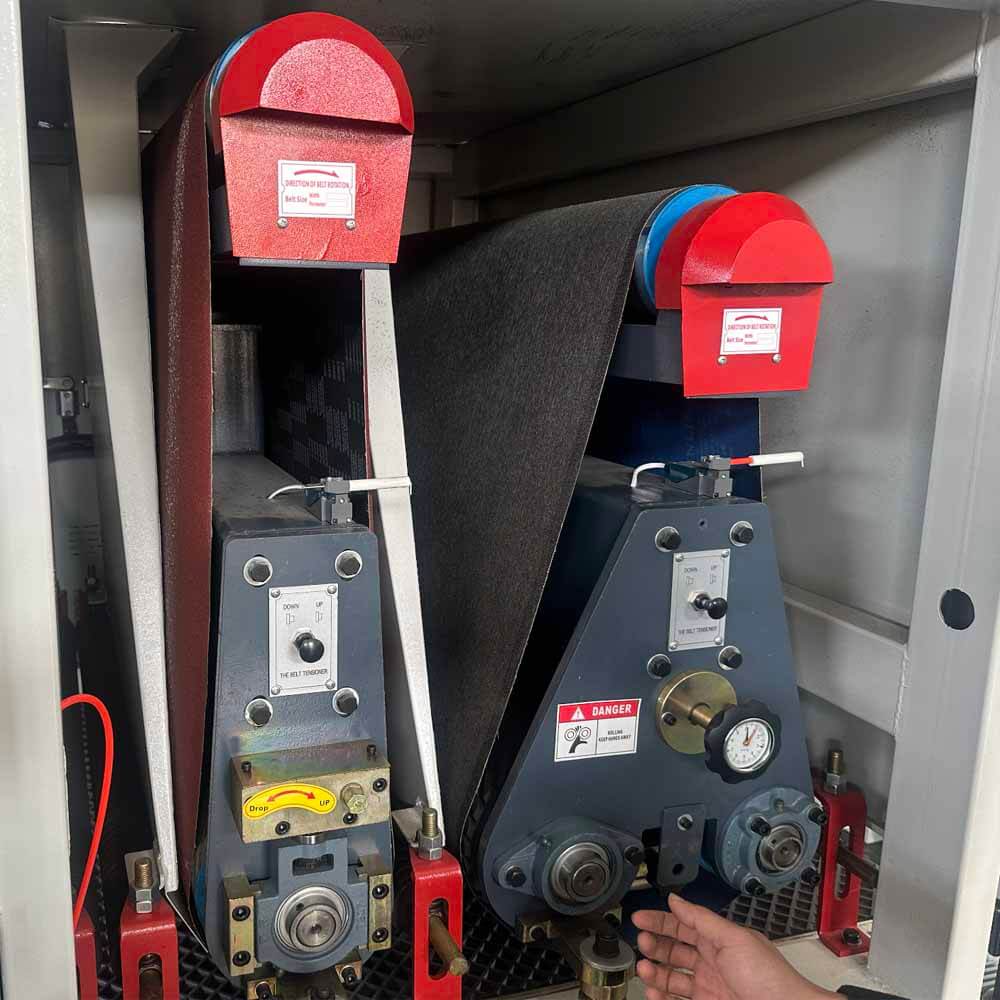
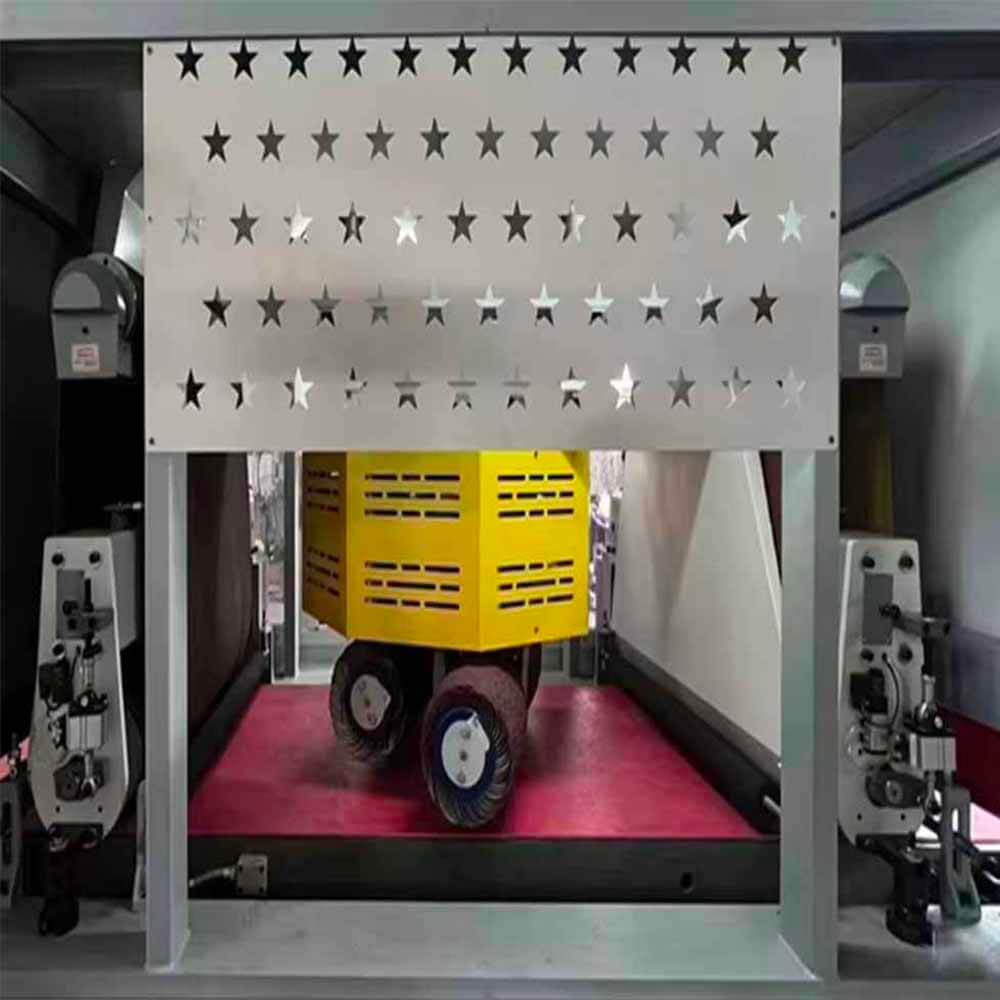
Special requirements: Rough grit + Chamfering grit + Fine grit
Applicable scenario: Complex workpieces that require leveling and edge treatment.
Configuration:
First pass: Rough sanding (40-80 grit belt) to remove surface imperfections and burrs.
Second pass: Chamfering sand (customized angle sanding belt), to deal with the edge transition, to ensure no sharp corners.
Third pass: fine sanding (180 grit sanding belt) to further optimize surface smoothness.
Characteristics: Suitable for shaped workpieces or processes that require high edge security
Basic combination: abrasive belt + chamfering wheel
Application scenario: surface treatment and edge finishing for simple workpieces.
Configuration:
First pass: coarse abrasive belt (40-80 grit), quickly removes burrs, weld marks and surface unevenness.
Second pass: chamfering wheel (standard angle), trimming edges, removing sharp corners, ensuring smooth and safe workpiece edges.
Characteristics: Economical and practical, suitable for preliminary processing of general metal products.
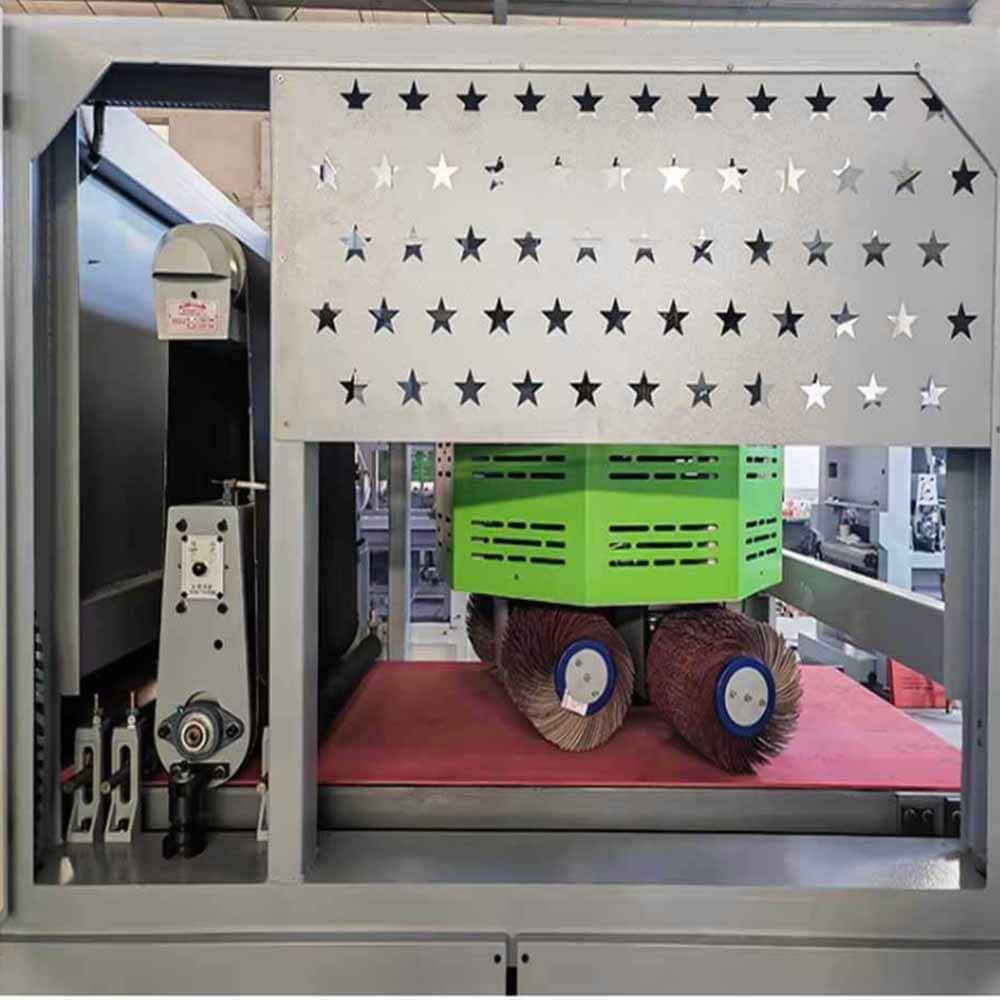
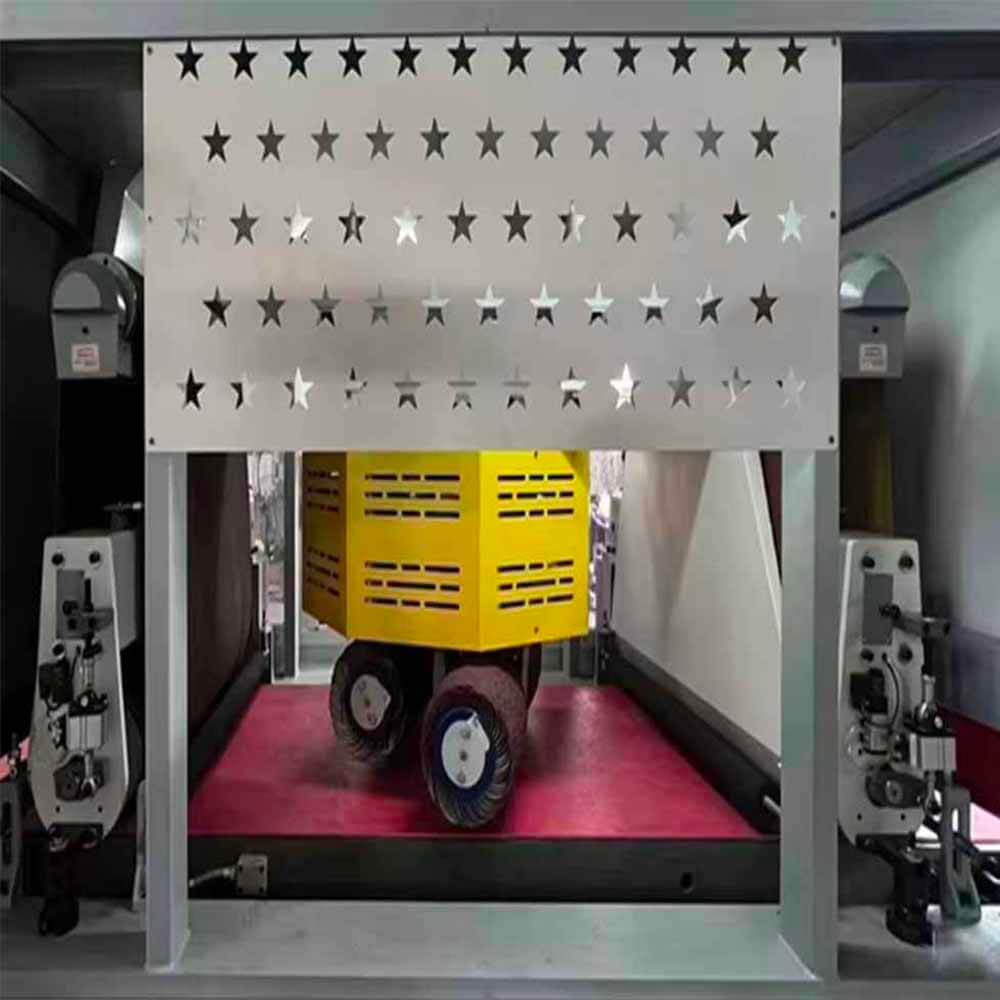
Standard combination: Rough sanding belt + Fine sanding belt + Chamfering wheel
Applicable scenarios: Processing tasks with high requirements for surface flatness and edge transition.
Configuration:
First pass: coarse sanding belt (40-80 grit) to clean up surface imperfections and burrs.
Second pass: Fine sanding belt (120-180 grit), refines the texture and eliminates the processing traces of the coarse sanding belt.
Third course: chamfering wheel (adjustable angle), rounding or beveling according to the design of the workpiece to ensure a natural edge transition.
Characteristics: Suitable for metal products with certain requirements on product appearance and safety.
Versatile combination: coarse sand + brushed sand + polishing wheel
Scenario: Workpieces requiring brushed texture and glossy effect, such as stainless steel appliance panels or architectural decorative parts.
Configuration:
First course: coarse sand (40-60 grit sand belt), remove burrs and initial leveling.
The second course: brushed sand (special brushed sand belt), to create a uniform and beautiful brushed texture.
Third course: polishing wheel (cloth wheel or wax wheel), to enhance the metallic luster of the textured area.
Characteristics: balancing functionality and decoration, suitable for the processing needs of the metal decoration industry.
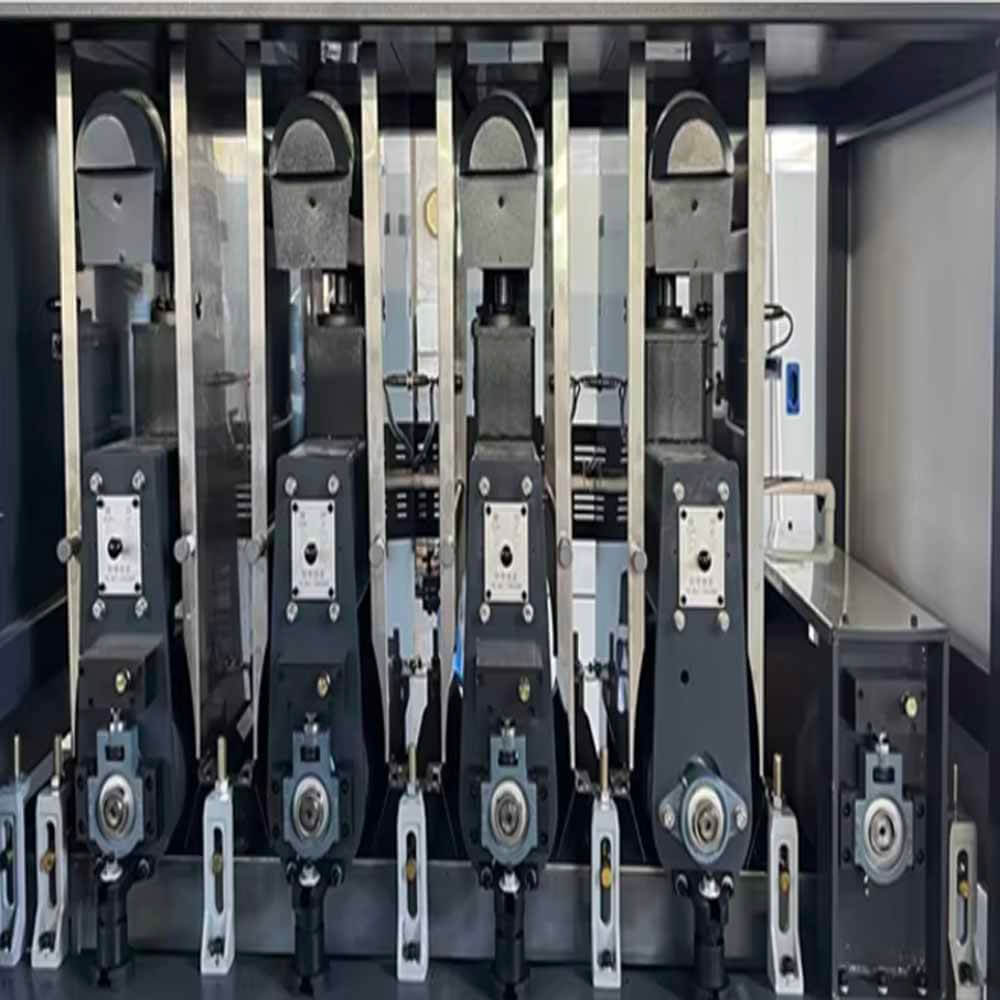
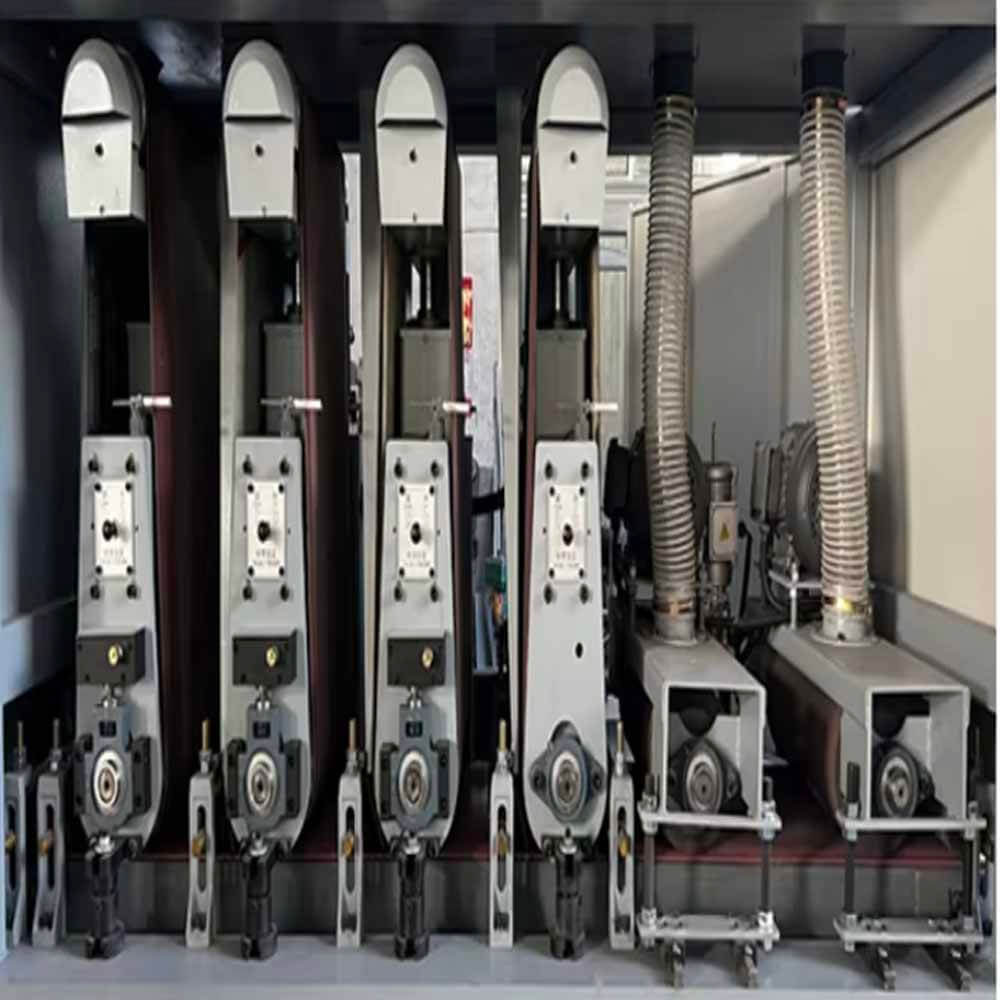
High-precision matching: fine grit + ultra-fine grit + polishing wheel
Applicable scene: High-end products that need high gloss and decorative effect.
Configuration:
First course: fine sanding (180 grit belt) to create a uniform and delicate surface.
Second course: super fine sand (240-400 mesh belt), to achieve a smooth effect close to the mirror surface.
Third course: polishing wheel (wool wheel or polishing paste wheel), giving a high gloss mirror effect.
Characteristics: Suitable for processing high-end products such as stainless steel kitchenware, elevator panels, and luxury metal parts.
Combination: Rough + medium grit + chamfering grit + polishing wheel
Scenario: Complex workpieces that need to be treated simultaneously for surface flatness, edge safety and luster.
Configuration:
First pass: coarse grit (40-80 grit belt) to remove large burrs and surface imperfections.
Second pass: medium grit (100-120 grit belt) to further optimize surface flatness.
Third course: chamfering sand (special abrasive belt), to deal with edge transition and ensure smooth edges without sharp corners.
Fourth pass: Polishing wheel (soft cloth wheel or polishing wax), giving the overall high gloss and exquisite appearance.
Characteristics: Suitable for comprehensive processing of shaped workpieces, high-end decorative parts or complex structural parts.
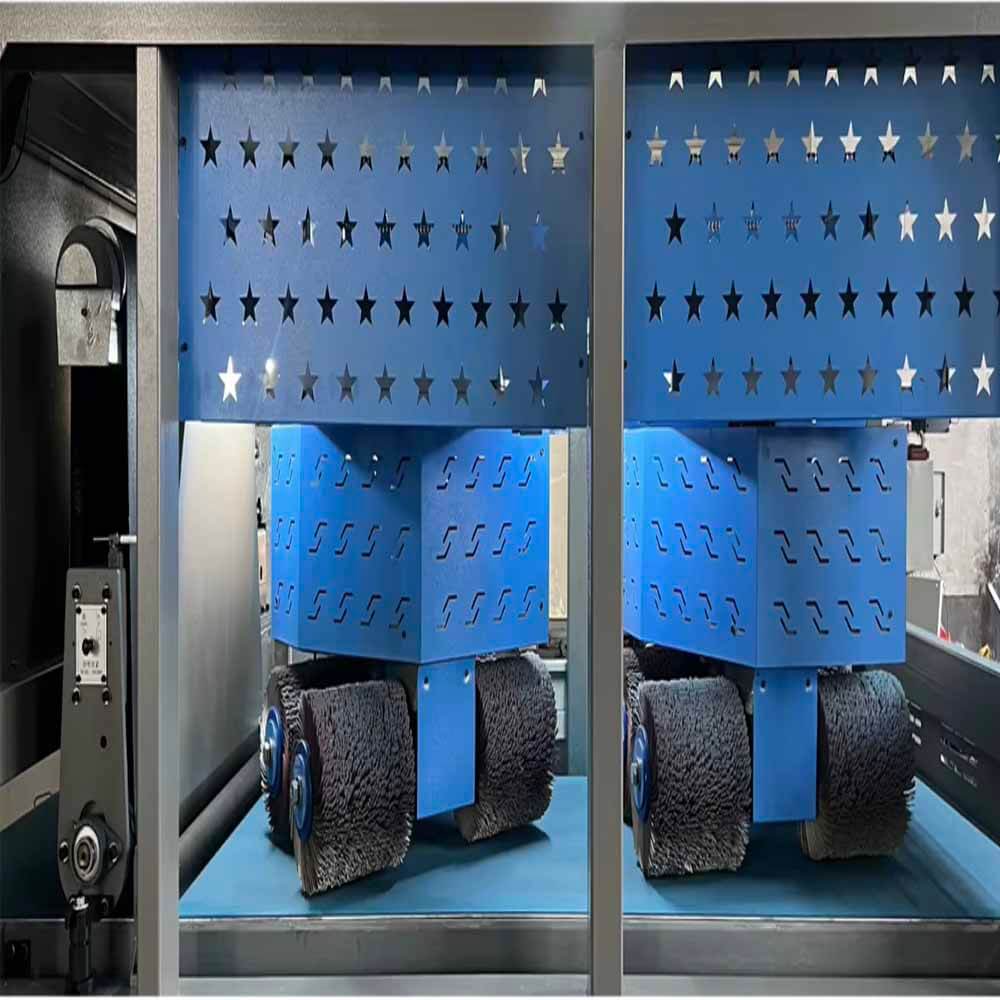